VideoRay employee Tim Good didn’t have to think twice when asked to help take up the fight against COVID-19.
“A longtime friend of mine called me and asked if I would join a group that was in urgent need of 500 protective face shields for first responders,” said Good, an engineering associate. The friend knew Good had access to two 3D printers at VideoRay and sent him a design file to produce the shields. “I started making the shields on March 29.”
Since then, Good and Steve Llewellyn, a sustainment engineer at VideoRay who personally owns a 3D printer, have cranked out dozens of the shields to donate to those locally on the front lines of the health crisis.
The shield was designed by Erik Cederberg and his coworkers at 3DVerkstan, a Swedish company.
The full-face visors are made with transparent acetate that’s attached to a headpiece. Good said it takes approximately two hours to make three shields. He and Llewellyn have contributed some of their own materials to the cause.
“It seems like the right thing to do,” Good said.
He noted that the 3D printers are usually used to make prototype parts for VideoRay’s remotely operated vehicles (ROVs), but they have worked well in producing the shields.
Good and Llewellyn are also looking into making protective masks for VideoRay employees, but that they’re in the experimental stage right now.
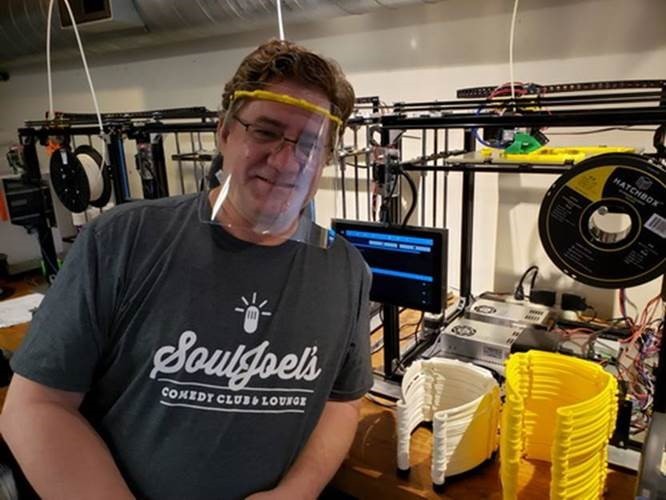